

The basic principle of spraying coating
Atomization process
The first step in spraying a coating is to atomize the paint or coating material. This is done with a spray gun or other spraying equipment. When the paint is sprayed from the spray gun, it is broken up into tiny droplets by high-speed airflow (such as compressed air) or other means (such as electrostatic, ultrasonic, etc.). The size and distribution of these droplets have an important effect on the quality of the coating. For example, in the process of automobile painting, the appropriate atomization can make the paint drops evenly distributed on the surface of the automobile body, forming a smooth and flat coating.
Depositional process
The atomized droplets are sprayed onto the surface of the coated object, where they deposit and form a coating. After touching a surface, droplets attach and accumulate in a variety of ways. In the case of liquid paint, the droplets fuse with each other, and as the solvent evaporates, the paint gradually solidifies to form a coating. For some powder coatings, the droplets need to be melted and solidified by heating and other means after deposition to form a continuous coating. For example, in the powder spraying of metal products, the deposited powder particles will melt and bond together after high temperature baking to form a protective and decorative coating.
Method of spraying coating
Air spraying
How it works: This is one of the most common spraying methods. The paint is blown out of the gun using compressed air to atomize and spray onto the surface. The spray gun usually has a paint container and an air nozzle, and the compressed air creates a high-speed airflow as it passes through the nozzle, bringing the paint out and atomizing it. For example, in furniture painting, air spraying can make the paint evenly distributed on the surface of the furniture, and obtain a smooth and beautiful effect.
Features: The advantage is that the equipment is simple, easy to operate, and can produce high-quality coatings, which are suitable for objects of various shapes and sizes. The disadvantage is that the paint utilization rate is low, because some of the paint will be dispersed with the air, and the spraying speed is relatively slow, and the spraying efficiency is not high for a large area.
Airless spraying
Principle: Airless spraying does not rely on compressed air to atomize the paint, but through a high pressure pump to pressurize the paint to a high pressure (usually about 10-30MPa), so that the paint through the small hole of the spray gun, due to the sudden drop in pressure and spray out. For example, when spraying waterproof paint on the exterior wall of a building, airless spraying can quickly spray the paint to a large area of the wall.
Features: The advantages are high spraying efficiency, can quickly cover a large area of the surface, and the paint utilization rate is higher than air spraying. The disadvantage is that the equipment is more complex, the need for high pressure pumps and other equipment, and the requirements for the operator are higher, because the high pressure paint may cause harm to the human body.
Electrostatic spraying
Principle: Electrostatic spraying is the use of electrostatic field to achieve coating spraying. In the spraying process, the coated object is grounded as the anode, the spray gun as the cathode, and the paint will be charged when sprayed. Due to electrostatic attraction, charged paint droplets are attracted to the surface of a grounded object, enabling efficient deposition. For example, in the coating of metal products, electrostatic spraying can make the paint uniformly adsorbed on the metal surface and reduce the waste of paint.
Features: The advantage is that the paint utilization rate is high, which can reach about 80%-90%, and the coating uniformity is good, especially for objects with complex shapes, because the electrostatic attraction can make the paint well attached to all corners of the object. The disadvantage is that the equipment cost is high, the equipment such as electrostatic generator needs to be equipped, and the electrical conductivity of the coating has certain requirements.
Powder spraying
Principle: Powder spraying is the powder coating is sprayed to the surface of the object through the spray gun or other equipment, and then the powder is melted and cured by heating to form a coating. Powder coatings are usually solid powders composed of resins, pigments, fillers, etc. For example, in the surface treatment of aluminum alloy doors and Windows, powder spraying can provide good weather resistance and decoration.
Features: The advantage is that the coating has good physical and chemical properties, such as high hardness, good wear resistance, strong corrosion resistance, etc., and the powder coating is an environmentally friendly coating, because it does not contain solvents, reducing the volatilization of organic solvents. The disadvantage is that special powder spraying equipment and high temperature curing equipment are required, and there are certain requirements for powder storage and treatment.
Factory Tour
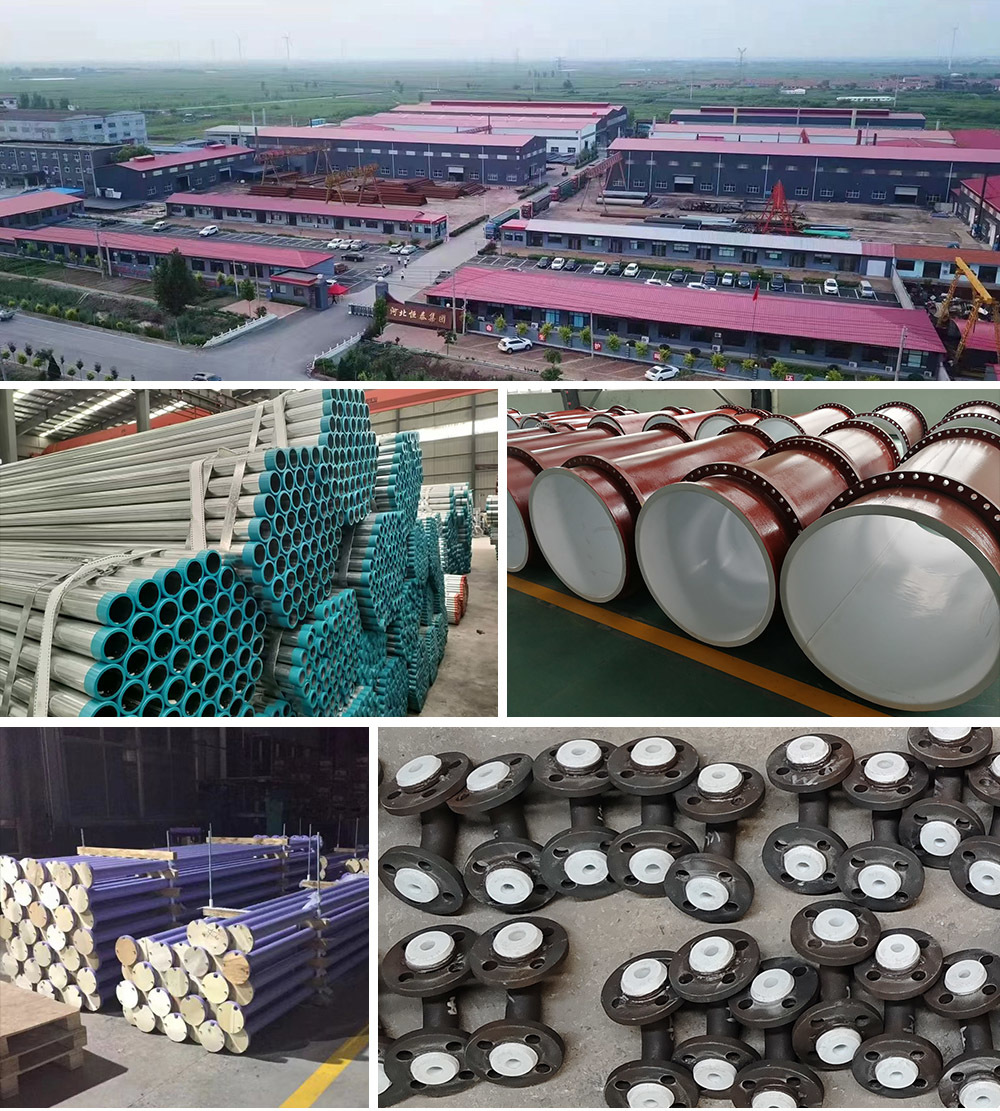
Enterprise Qualification
Keywords


Sprayed PTFE/PFA corrosion-resistant pipeline and fittings
Contact Us
Classification