


A reducer is a type of pipe fitting used to connect pipes of different diameters, widely applied in industries such as petroleum, chemical, metallurgy, power, construction, and environmental protection. Below is a detailed introduction:
1. Definition
A reducer is used to connect two pipes with different diameters, ensuring smooth flow of media.
2. Classification
Concentric Reducer: The centerlines of both ends coincide, suitable for vertical installation.
Eccentric Reducer: The centerlines of both ends do not coincide, suitable for horizontal installation to prevent the accumulation of gas or impurities.
3. Materials
Common materials include:
Carbon Steel: Suitable for general working conditions.
Stainless Steel: Corrosion-resistant, used in chemical and food industries.
Alloy Steel: Resistant to high temperature and pressure, used in power and petrochemical fields.
Plastic: Corrosion-resistant, used in chemical and environmental protection industries.
4. Manufacturing Processes
Forging: Suitable for high-pressure and high-temperature environments, with high strength.
Casting: Suitable for complex shapes, with lower costs.
Welding: Suitable for large-diameter and thick-walled reducers.
5. Connection Methods
Welding: Suitable for high-pressure and high-temperature environments, with good sealing.
Flange Connection: Easy to disassemble and maintain.
Threaded Connection: Suitable for small-diameter and low-pressure pipelines.
6. Application Fields
Petrochemical Industry: Transporting oil, gas, water, and other media.
Power Industry: Transporting steam, water, and other media.
Construction: Water supply, drainage, and HVAC systems.
Environmental Protection: Sewage treatment and exhaust gas emission systems.
7. Common Specifications and Sizes
Reducers are available in a variety of specifications and sizes to meet different application needs. Common specifications include:
Diameter Range: Typically from 1/2 inch to 48 inches or larger.
Wall Thickness: Varies based on pressure requirements, often following standards like SCH40, SCH80, etc.
Length: Standard lengths are available, but custom lengths can be provided based on requirements.
8. Customization Based on Customer Requirements
Reducers can be customized to meet specific customer needs, including:
Special Materials: Such as titanium, nickel alloys, etc., for highly corrosive or high-temperature environments.
Non-Standard Sizes: Tailored to unique pipeline configurations.
Special Coatings or Linings: For enhanced corrosion resistance or specific media compatibility.
Unique Connection Types: Such as grooved, clamped, or other specialized connections.
9. Selection Considerations
Media Characteristics: Consider corrosiveness, temperature, pressure, etc.
Pipe Diameter: Choose the appropriate size based on actual needs.
Installation Environment: Consider space, temperature, humidity, and other factors.
Material Selection: Choose the appropriate material based on media characteristics and environment.
10. Maintenance and Care
Regular Inspection: Check for corrosion, wear, cracks, etc.
Cleaning: Regularly clean internal impurities to prevent clogging.
Corrosion Protection: Take anti-corrosion measures to extend service life.
11. Standards and Specifications
National Standards: Such as GB/T 12459, GB/T 13401, etc.
International Standards: Such as ASME B16.9, DIN 2616, etc.
12. Common Issues
Leakage: Often caused by improper installation or aging sealing materials.
Corrosion: Due to corrosive media or humid environments.
Clogging: Due to impurities in the media or untimely cleaning.
Summary
Reducers are indispensable components in pipeline systems. Proper selection, installation, and maintenance are crucial for the normal operation of the system. With a wide range of standard specifications and the ability to customize based on customer requirements, reducers can be tailored to meet the specific needs of various applications.
Factory Tour
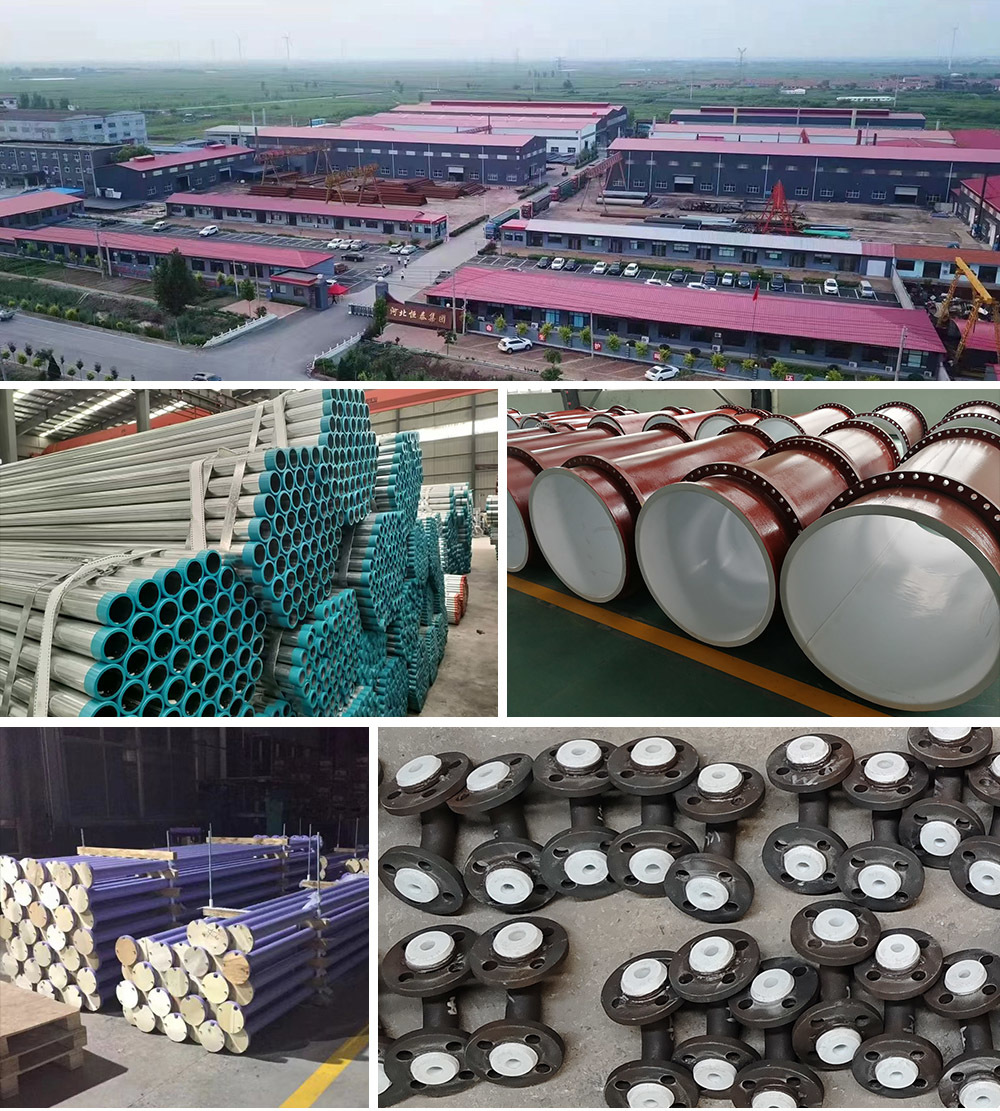
Enterprise Qualification
Keywords



Concentric Reducer Eccentric Reducer Pipe Fittings
Contact Us
Classification